It's quite easy to be amazed by the sight of a World Rally Championship automotive racing down narrow asphalt paths, sliding between snow drifts and surviving a few of the most difficult rocky terrain on the earth. But how exactly are these machines built?
Hyundai Motorsport took a behind-the-scenes take a look at the method behind the development of the €200,000 i20 N Rally2 automotive that competes in WRC2 and won back-to-back European Rally Championship titles under Hayden Paddon.

Regardless of the discipline, racing and rally cars are built with great care – assembling a life-size Meccano or Lego set, consisting of roughly 3,000 parts, is an actual art. This is a process that Hyundai has perfected to find a way to provide 30-50 cars a yr at its workshop in Alzenau, Germany.
“To build a Rally2 car, we need around 200 hours, and each car generally has two or three mechanics working on it, which means we can produce a car in two weeks,” explains Benoit Nogier, Hyundai customer racing manager. “In Rally1 there are a number of parts that must be fitted to the tubular chassis, they usually are far more specific – they don't use any standard parts. We don't have many standard parts within the automotive, but every thing is designed for them anyway, and a hybrid takes a number of time. When a hybrid is involved, there can't be as many individuals working on the automotive, so it takes at the very least 100 hours longer to construct the automotive than it could for a Rally2 automotive.
Perhaps unlike other motorsports, rally cars are specifically designed for quick assembly and disassembly, so components might be replaced during timed services. This implies that the four-wheel-drive i20 N Rally2, based on the road-going i20 N, requires modifications. The rally automotive shares roughly 25% of its components with the road automotive, although some are adapted.
“A standard car is not built and designed with assembly and disassembly in mind, as is the case with rally cars,” notes Nogier. “For example, the sunshine on the front of a automotive is designed to be reinstalled a few times during its life. In our case, we now have to do that process sometimes two or 3 times a day. We need to switch the parts to what we want. If we kept the usual electrical connectors, this wouldn't work.
“It's an enormous a part of the project and due to experience we all know which parts we are able to use. It takes a number of work to regulate every thing, but we all know what we now have to do.
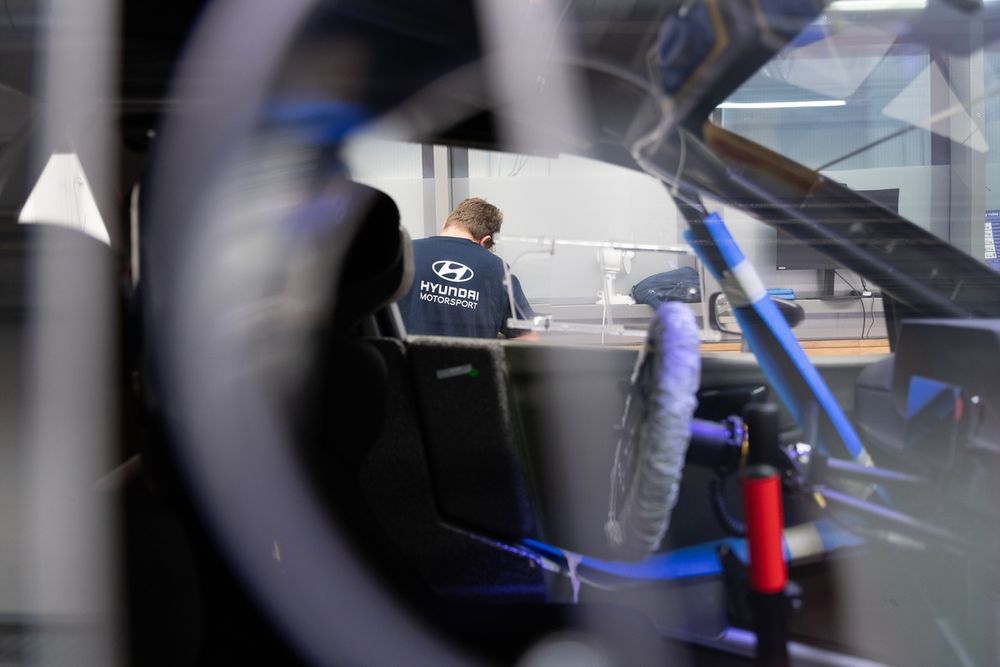
Installing a dashboard is probably the most complicated tasks
Photo: Hyundai Motorsport
Hyundai divided the development of the asphalt i20 N Rally2 into 40 stages – it’s a process that might be done watched in a YouTube video.
Building a Rally2 automotive starts with a bare road automotive chassis, which is fitted with a roll cage after which painted. This takes place before the installation of components reminiscent of the fuel tank (80 liters) and all electrical installations and internal components, including the dashboard, steering column, center console and washer reservoir. A key a part of the method is the mass pre-assembly of components to enhance performance. These components can then be easily installed, which may take 15-Half-hour, depending on the part.
“When we receive the body, we usually anticipate certain components from the components, so that, for example, the hubs are ready to be installed on the car, the subframes are ready, the gearbox is ready and the engine is ready,” Nogier states.
“The engines come from the factory completely standard and we make modifications such as new pistons etc.” Benoit Nogier
“The first two steps are to put in the brake lines after which install the wiring harness. Then we add every thing needed for the driving force and passengers contained in the automotive, in addition to spare wheels. Then we now have every thing pre-assembled, with the front and rear axles, subframe and gearbox, and ending with the front and rear bumpers.
“For example, a week later we will decide to work on the front axles and assemble 10-15 front axles, and a week later we will do the same with the rear axle. We try to anticipate a bit and try to have some pre-assembled car parts in stock to make it easier. This way we can maintain the same level of quality.”
Interestingly, the element that takes the longest to suit right into a automotive, based on Nogier, is the dashboard: “It's quite a big part and it must be adapted to the cars. Not all of the dashboards we receive from the supplier are the exact same, so you’ve to adapt to the bodywork, and this takes a while.
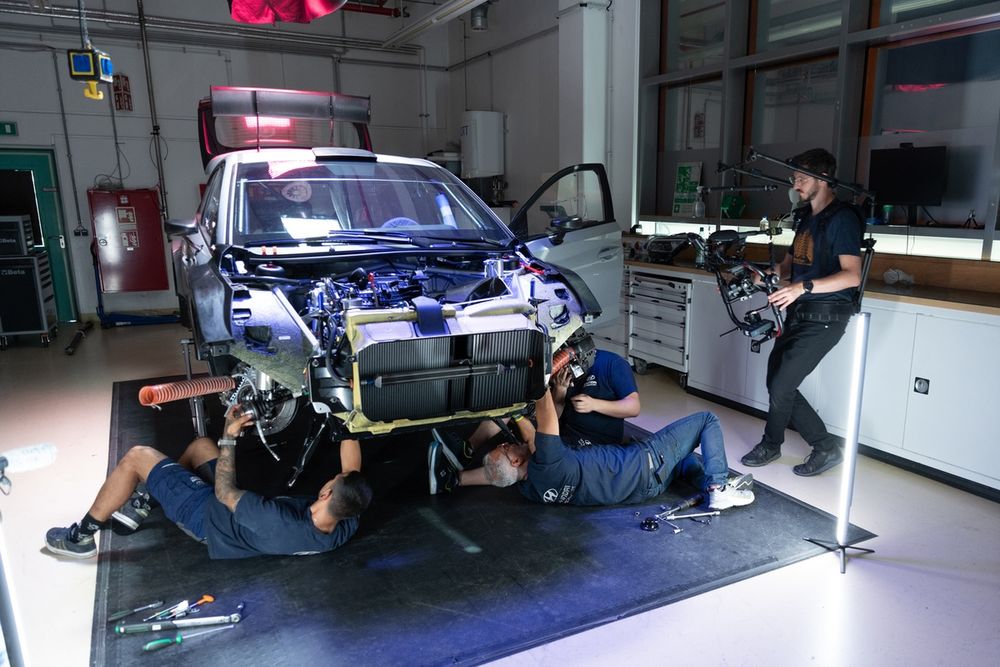
Engine installation is one other key milestone
Photo: Hyundai Motorsport
The next 10 steps involve further work on the automotive's interior, during which the seats, seat belts, steering wheel and fire extinguisher – an FIA safety requirement – are bolted on. Once accomplished, the work moves to the outside of the automotive, where the hind lights, tailgate, rear fender and front doors are installed. These body panels, minus the rear wing, are standard. Only the front and rear bumpers and wheel arches were specially designed and fabricated from lightweight composite fiberglass or carbon fiber.
This is where the automotive's 1.6-liter turbocharged four-cylinder engine with a capability of 285 hp is installed, together with a five-speed sequential gearbox.
“The engines come completely standard from the factory and we make modifications such as new pistons etc.” – Nogier tells us. “The engine block and cylinder are very close to standard. The rest is modified. The engine will then go on the dyno to make sure the performance level is where we want it to be. After the engines are delivered to us, we pre-assemble all the connected parts so that the starter, alternator and engine emerge. Then we install the clutch and gearbox and the car is ready to drive.”
Once the engine was installed, it was time to put in the rear doors and the ability steering pump and alternator – the latter being considered one of only two parts, together with the starter motor, which are taken entirely from the road automotive. The all-important pre-assembled radiator and cooling assembly, vital to deal with the extraordinary conditions the automotive faces in the course of the stages, is then fitted, before the front and rear subframes (one other pre-assembled component), exhaust system and driveshaft are fitted.
“The first challenge is to organize yourself and find the best process that will be most effective, but with experience it becomes quite logical,” says Nogier. “I would say the biggest challenge is maintaining the same level of quality because the mechanics are not always the same and the parts are not always exactly the same, but the quality has to be the same.”
This is where the Hyundai i20 N Rally2 really starts to take shape for the ultimate series of 10 steps.
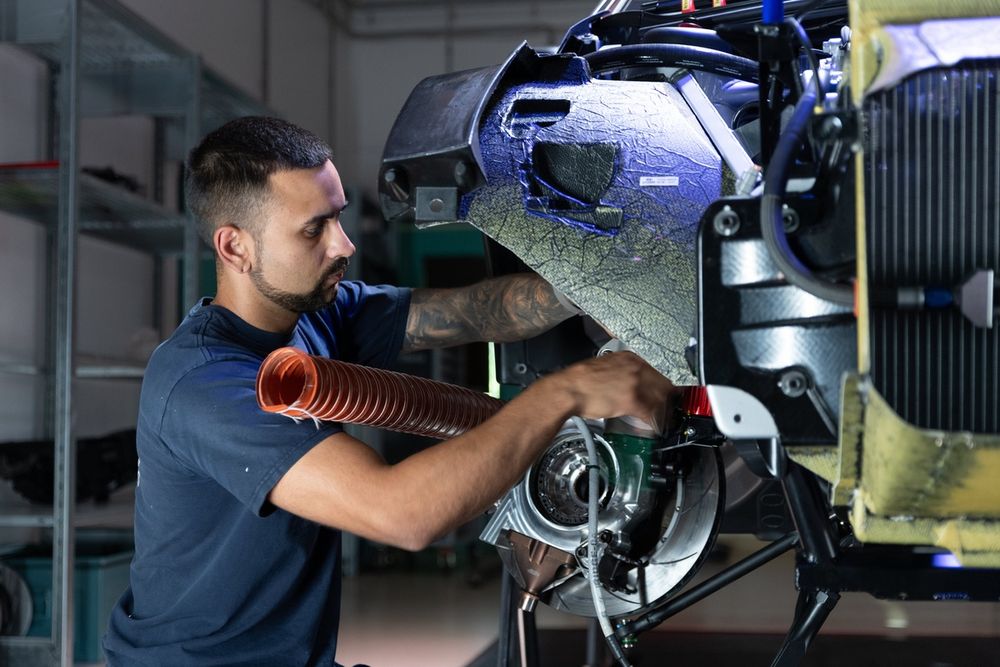
Suspension and brakes are critical components
Photo: Hyundai Motorsport
The final pieces of this complex mechanical puzzle mainly deal with the outside, starting with the three-way adjustable front and rear McPherson shock absorbers – probably the most refined and crucial elements of any rally automotive. For the needs of this exercise, the automotive in query is an asphalt model, but customers have the choice to configure components reminiscent of suspension and brakes to compete in gravel conditions.
Next on the to-do list are the uprights, followed by ventilated brake discs (355mm diameter for asphalt on this model) with four-piston calipers. Before checking the systems, the rear anti-roll bar, front grill and bumpers, and 18-inch wheels are installed before the engine is first began.
No matter what number of cars roll off the production line, the primary firing of a accomplished automotive still gives a singular sense of satisfaction to those that construct these advanced machines that may withstand the harshest conditions.
“We love this job and seeing the car start for the first time is always a nice moment for all of us. It's like seeing a newborn baby!” Benoit Nogier
“We love this job, and seeing the car start for the first time is always a nice moment for all of us,” Nogier smiles. “We have been in this business – some of us for 20 years – and every time they start a car for the first time there is always a certain excitement. It's like seeing a newborn baby!”
Transforming a body right into a rally automotive in two weeks is not any mean feat, but can this already clever process grow to be much more efficient in the longer term? “We are much better organized during reassembly than in the past,” adds Nogier. “I feel up to now it was something like, 'we construct a automotive after which we construct one other and one other.' Now we're attempting to predict production a bit more for the subsequent six months. We have a broader vision.
“I feel we now have reached a certain point and I don't see this process changing in the longer term. The only thing that may change is a change in technology, so if we moved to totally electric or hybrid vehicles, a bit more people and processes would must be introduced into the production of the automotive, but I don't see that taking place.”
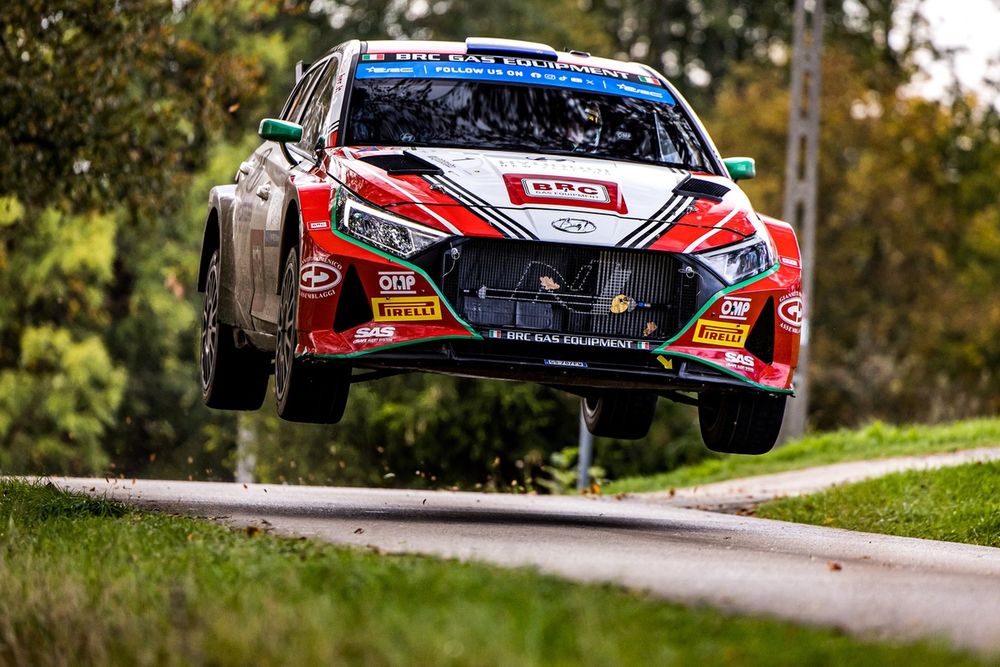
The Hyundai i20 N Rally2 won the ERC again with Paddon
Photo: Red Bull Content Pool
In this text
Tom Howard
WRC
ERC
Hyundai Motorsport
Be the primary to know and subscribe to email updates with real-time news on these topics
Subscribe to news notifications